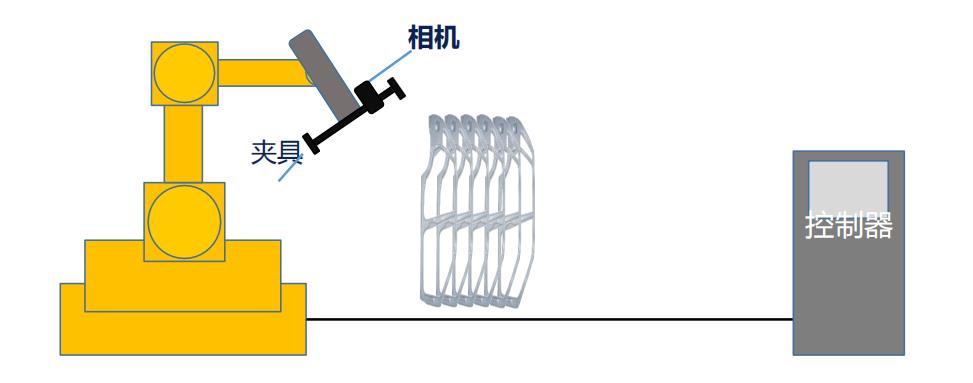
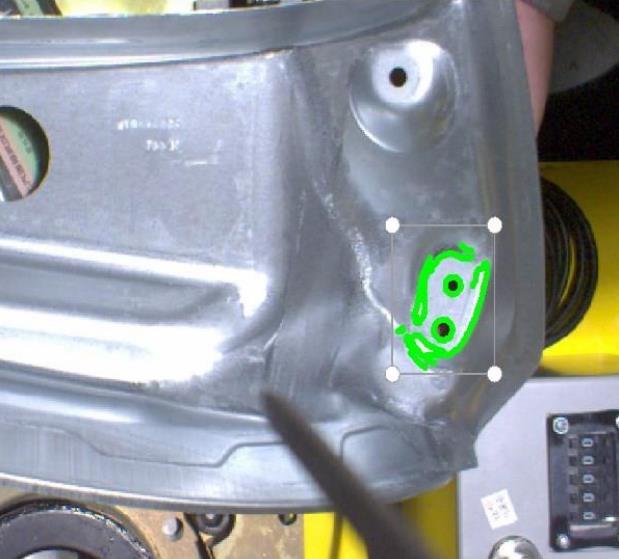
Grab Guide
• 3D vision guided robot grasping workpiece
• Support initial position tolerance of up to 70mm and 10 °
• 0.5 mm for maximum accuracy
• Automatic guided hand eye calibration
• Complete the template setting of new model in half an hour
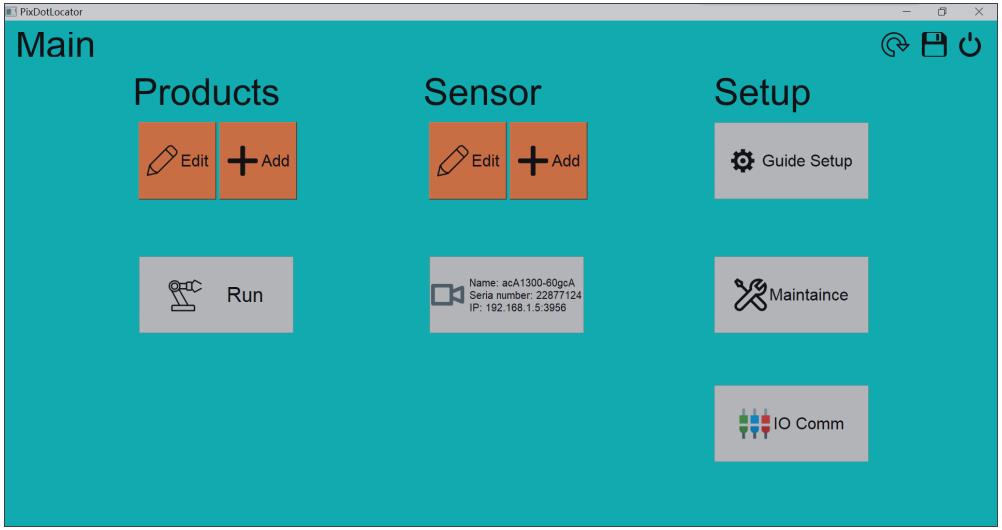
software function
• Unified hardware management (camera, light source)
• Automatic guided hand eye calibration
• Automatic template extraction
• History tracing function
• Maintenance and communication test mode
Automatic hand eye calibration
Teaching aids
Intelligent contour extraction
History tracing function
Template quality assessment
Data statistics function
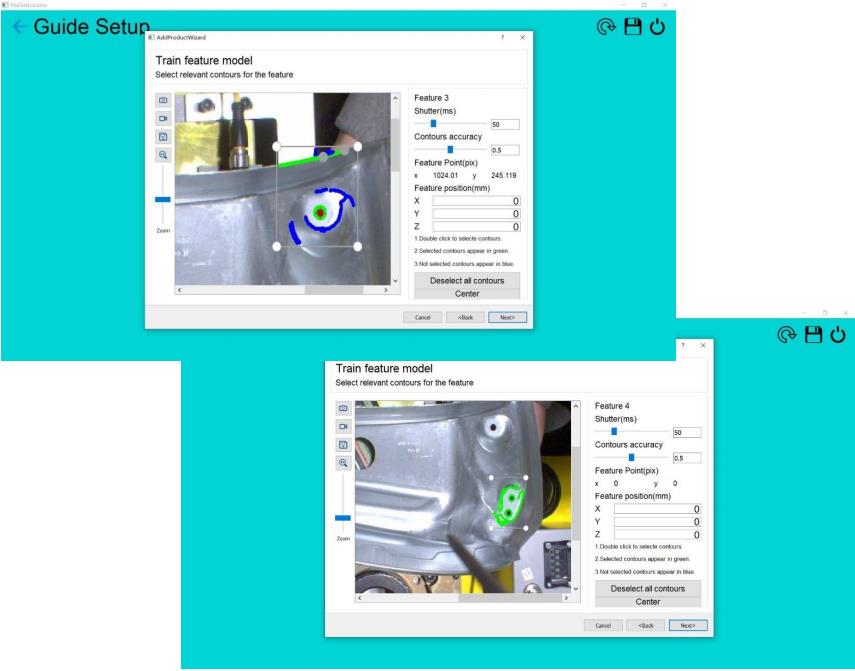
Introduction to teaching
For each kind of parts that need to be grasped, a separate template should be set up. The software can automatically recognize the part features when making the template. During production, the software will compare the 3D position of the material with the template difference to guide the robot to grasp.
characteristic
The software will automatically extract the best features by using the selection tool box to select through holes, edges and other areas.
After the template is made, the software will automatically evaluate the template quality.
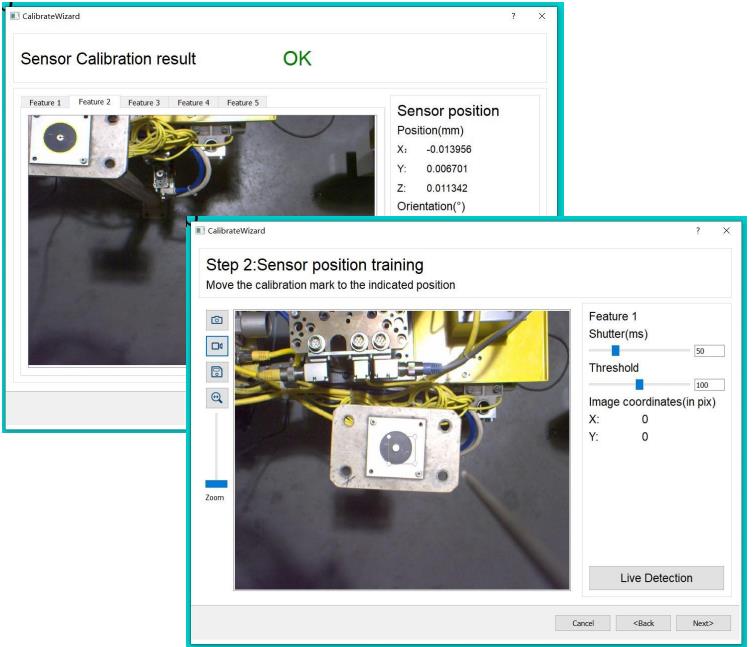
hand-eye calibration
The camera position needs to be calibrated after the camera is newly installed or the camera position is changed. Under the guidance of software, the mobile robot can complete the calibration by photographing the calibration board from five angles.
characteristic
The software recommends the best shooting position to maximize the calibration success rate.
Complete the calibration configuration within 10 minutes.
NO. | Device name | Specifications |
1 | Camera | - camera with 6mm,8mm,12mm Lens - Strobe light source |
2 | Vision System | - 2.5D Robot Guidance - Automatic hand-eye calibration - Teaching - Historical tracing |
3 | Controller
| - IPC 610 - CPU i5-6500 - 2 Gigabit Ethernet port - 8G RAM - 2T Hard disk - Win7 64bits |
4 | Cabinet | - Size H×W×D:1800×600×600 - Air conditioning |
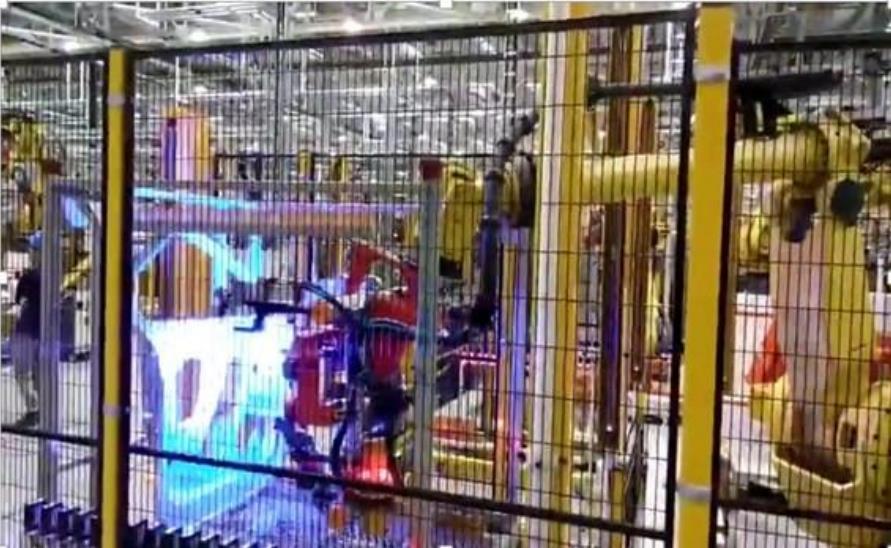
Application cases